PROFIBUS
Throughput is supported by world-leaders in industrial data communications equipment which is backed by extensive research and development and field tested, offering warrantees and and backup service that is worldclass.
PROFIBUS Protocols
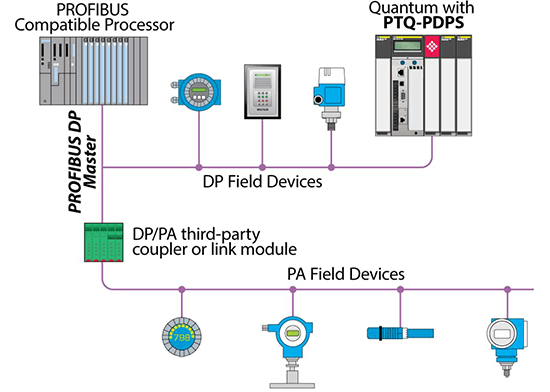
PROFIBUS
(Process Field Bus) is a standard for fieldbus communication in automation technology and was first promoted in 1989 by the German Department of Education and Research and then adopted and used by Siemens. It initially comprised different types of Profibus (DP & FMS). DP is described below. FMS was originally developed for inter PLC communications but was complex to use and became superfluous once Ethernet options became popular to connect PLCs together.
PROFIBUS DP (Decentralized Peripherals) is used to operate sensors and actuators via a centralized controller in production and factory automation applications. It is based on serial RS-485 standards, although it does have some special diagnostics and timing adaptions built in to ensure security and speed of transfer of data. The controller is the master to the peripheral slaves. All data is transferred via the master.
PROFIBUS DP uses two core screened cable with a violet sheath, and runs at speeds between 9.6kbit/s and 12Mbit/s. A particular speed can be chosen for a network to give enough time for communication with all the devices present in the network. If systems change slowly then lower communication speed is suitable, and if the systems change quickly then effective communication will happen through faster speed. The RS485 balanced transmission used in PROFIBUS DP only allows 126 devices to be connected at once; however, more devices can be connected or the network expanded with the use of hubs or repeaters.
There are a number of baud rates used, ranging from 9.6kbits through to 12Mbits, a total of 128 nodes (network connections) can be implemented per network but need to be in segments of 32 nodes. In the case of segmentation, repeaters are used to divide the network into workable segments.
View our Profibus ProSoft Range of products - Click here.
PROFIBUS PA
Profibus for Process Automation: is used to monitor measuring equipment via a process control system in process automation applications. This variant is designed for use in explosion/hazardous areas (Ex-Zone 0 and 1). The Physical Layer (i.e. the cable) allows power to be delivered over the bus to field instruments, while limiting current flows so that explosive conditions are not created, even if a malfunction occurs. The number of devices attached to a PA segment is limited by this feature. PA has a data transmission rate of 31.25 kbit/s. However, PA uses the same protocol as DP, and can be linked to a DP network using a coupling device. The much faster DP acts as a backbone network for transmitting process signals to the controller processor. This means that DP and PA can work tightly together, especially in hybrid applications where process and factory automation networks operate side by side.
PROFIBUS PA is slower than PROFIBUS DP and runs at fixed speed of 31.2kbit/s via blue sheathed two core screened cable. The communication may be initiated to minimise the risk of explosion or for the systems that intrinsically need safe equipment. The message formats in PROFIBUS PA are identical to PROFIBUS DP.
Note: PROFIBUS DP and PROFIBUS PA should not be confused with PROFINET.